The procedure of CNC machining entails the usage of a computer system to manage maker tools for a more trusted and regular output. This modern technology translates CAD (computer-aided style) versions directly right into machine-readable code, which guides the machining procedure. The outcome is that manufacturers can generate components with constant top quality and accuracy, minimizing waste and the threat of error in manufacturing. When it comes to copper, which can be rather tough to device as a result of its thermal conductivity, high ductility, and tendency to work-harden, CNC innovation gives the versatility needed to resolve these concerns successfully. Specialized devices and techniques are often utilized to maximize the machining process, which can consist of making use of reducing devices coated with hard products to decrease wear and boost performance when collaborating with soft steels like copper.
Discover copper cnc machining just how copper CNC machining combines innovative technology with lasting techniques to generate intricate, high-precision components, driving development throughout markets such as electronic devices, auto, and aerospace.
Amongst the primary advantages of CNC machining copper is the capacity to generate intricate forms that standard machining approaches might not accommodate. The high precision achievable with CNC innovation permits manufacturers to create tightly toleranced functions that are vital in several applications. In the electronics industry, as an example, the demand for elements with very little tolerances is vital, as digital gadgets end up being smaller sized and a lot more elaborate. CNC machining helps with the production of micro-components with such fine tolerances, allowing improvements in wise gadgets, wearable modern technology, and various other customer electronics. Furthermore, the repeatability of the CNC machining process makes certain that automation of copper components preserves uniformity, hence fulfilling rigorous sector criteria.
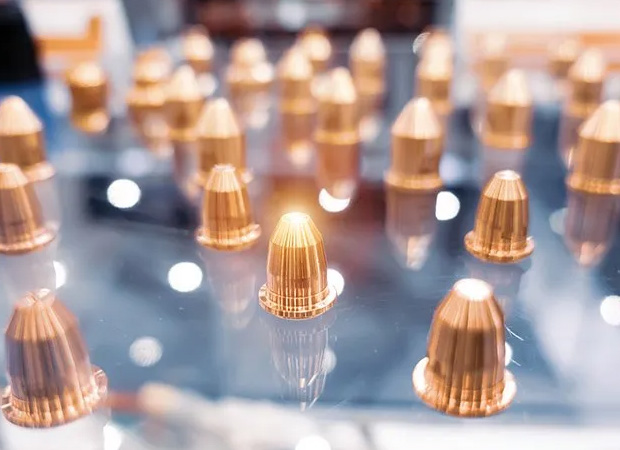
Temperature level administration plays an important role in the CNC machining of copper due to its capacity to perform warmth quickly. High-speed machining can result in significant warm generation, which may adversely affect the buildings of the copper and aggravate device wear. As a result, CNC machinists frequently transform to innovative air conditioning techniques, such as flood coolant systems and haze lubrication, to handle warm and extend device life. By controlling the temperature level throughout machining, manufacturers can attain much better surface coatings, boost accuracy, and produce get rid of enhanced mechanical properties. Furthermore, with the introduction of technologies like high-pressure air conditioning systems and ingenious reducing liquid formulations, CNC machining can attain ideal performance while appropriately taking care of thermal impacts.
The sustainability facet of CNC machining copper is not to be neglected. Copper is a highly recyclable product-- recycling copper needs up to 90Discover countersink size chart just how copper CNC machining merges sophisticated technology with lasting practices to generate intricate, high-precision parts, driving development throughout industries such as electronics, auto, and aerospace. less energy than mining and refining new copper ore. CNC machining, paired with sustainable techniques, can decrease waste by permitting manufacturers to use scrap copper from other procedures. The integration of reusing and environment-friendly methods right into machining processes straightens with the progressively eco-conscious worths of sectors and consumers alike. As organizations aim to lower their carbon footprint and enhance their environmental stewardship, CNC machining can play a necessary role in assisting in these objectives by supporting recyclable products circulation within the supply chain.
In enhancement to sustainability, cost-effectiveness is an additional crucial aspect for manufacturers selecting CNC machining for copper parts. Though the initial investment in CNC equipment may be substantial, the long-lasting advantages can outweigh the expenses. CNC machining offers a decrease in labor prices due to its automatic nature and reduces the demand for extensive manual intervention. The exact control & repeatability supplied by CNC technology reduces scrap rates, reducing product prices. In addition, for small to medium batch production runs, CNC machining can verify extra economical compared to conventional machining procedures, as it permits for smooth changes and layout changes without extensive retooling. This capability to pivot swiftly can be useful, particularly in fast-paced industries where market demands can move suddenly.
As innovation develops, the functionalities within CNC systems are expanding, even more enhancing the capabilities of copper machining. The integration of simulation software allows manufacturers to anticipate possible concerns prior to the machining process begins. These simulations enable better preparation of device courses and illuminate exactly how the copper material will respond throughout the machining procedure. By recognizing and resolving prospective difficulties in advancement, companies can minimize downtime and rise performance, producing a smoother functional circulation.
Education and learning and experience in CNC machining are essential for recognizing the full potential of copper procedures. Proficient machinists should be proficient in analyzing style specifications, selecting the ideal devices, and adjusting machining parameters to minimize concerns related to copper's special machining qualities. Furthermore, the innovation of additive production modern technologies, such as 3D printing, has developed new paradigms in the handling of copper. Crossbreed machining, which integrates conventional CNC machining methods with additive production, is emerging as a sensible technique for producing detailed copper components, mixing the staminas of both technologies and possibly reinventing how suppliers come close to copper production.
In the realm of research study and growth, CNC machining is aiding the exploration of brand-new copper alloys to boost performance even more. As worldwide sectors work toward higher power efficiency, copper's function as a conductor in digital circuits will certainly remain critical, driving need for innovative machining services.
The aerospace and vehicle sectors are additionally keen adopters of copper CNC machining, especially where light-weight parts are of crucial value. The mix of copper's light-weight nature and excellent electrical and thermal conductivity makes it a suitable selection for components such as electrical get in touches with, warm exchangers, and circuitry systems. As the shift toward hybrid and electric automobiles proceeds, the need for high-performance copper components will likely surge, consequently driving the need for advanced CNC machining practices that guarantee effectiveness and top quality in manufacturing. From a production standpoint, the ability to innovate quickly and provide precision-engineered components comes to be significantly essential in tackling the emerging demands of these fast-evolving industries.
As CNC machining technology remains to develop, it permits more automation, where basic procedures such as device modifications, assessments, and maintenance can be configured into the production cycle. This evolution suggests that suppliers will certainly have the ability to accomplish higher productivity degrees, much shorter preparations, and higher flexibility in accommodating custom demands or variants in style. As a result, companies that engage in CNC machining procedures are much better fit to pivot in response to the changes in customer and market needs, fostering growth in a significantly affordable landscape.
Discover countersink size chart just how copper CNC machining combines sophisticated technology with sustainable techniques to generate detailed, high-precision parts, driving advancement across industries such as electronic devices, vehicle, and aerospace.
The worldwide marketplace for CNC machining of copper is experiencing considerable development, influenced by factors such as the surge of smart modern technologies, electric vehicles, and continuous efforts to boost energy performance across numerous applications. In this training, ability and evolution advancement remain vital; investing in labor force education on CNC machining methods, innovations, and product sciences will certainly encourage producers to remain ahead of the contour.
Finally, the assimilation of CNC machining with copper materials uses a distinctive one-upmanship for makers in today's fast-paced commercial landscape. Its ability to provide high accuracy, decrease manufacturing time, and enable complicated layouts makes CNC machining a crucial component of contemporary production practices. Combined with sustainability efforts, cost-effectiveness, and chances for technology, the CNC machining of copper not only satisfies the needs of contemporary applications yet also prepares for the future trajectory of production in multiple markets. As sectors develop and the borders of technology broaden, welcoming CNC machining's potential will be vital to realizing unmatched development and innovation in the use of copper items. The synergy of copper's material residential properties with advanced CNC machining methods proclaims a brand-new age in which sustainability, effectiveness, and accuracy work hand-in-hand to produce cutting edge components that will define the future of manufacturing and past.